Metal Fabrication Melbourne: Accuracy Design for All Requirements
Metal Fabrication Melbourne: Accuracy Design for All Requirements
Blog Article
Top Methods for Optimizing Steel Manufacture Processes for Optimum Efficiency
In the realm of steel construction, the pursuit of effectiveness is a perpetual goal that drives market professionals to discover cutting-edge approaches and technologies. As the need for accuracy and rate heightens, business are urged to review their manufacture processes continually. From careful design intending to accepting cutting-edge technologies, the pursuit for optimal effectiveness in steel fabrication entails a multifaceted technique. By executing top strategies customized to optimize procedures, organizations not just improve productivity but additionally elevate the high quality of their output. Allow's discover just how these approaches can reinvent steel construction processes, leading the method for extraordinary performance and competitiveness in the sector.
Efficient Format Planning
In the world of steel fabrication processes, tactical and effective format preparation plays an essential role in enhancing production process and maximizing functional productivity. The format of a steel construction center directly affects the performance of procedures, product flow, and employee efficiency. By thoroughly creating the setup of machinery, workstations, storage areas, and product handling tools, companies can dramatically minimize unneeded activity, reduce material taking care of times, and optimize the total production process.
An efficient format strategy considers variables such as operations series, closeness of workstations, product handling paths, and security laws. It intends to develop a rational and structured circulation of activities from raw material consumption to the final item dispatch. Through effective layout preparation, business can remove traffic jams, decrease manufacturing downtime, and improve the total functional effectiveness of the steel fabrication process.
Furthermore, a well-thought-out format strategy allows better usage of readily available space, boosted communication in between employees, and enhanced safety methods within the center. In general, investing time and sources in creating a reliable layout plan can produce considerable benefits in terms of raised performance and cost savings for steel fabrication organizations.
Advanced Cutting Technologies
Utilizing sophisticated technologies in steel construction procedures enhances precision, effectiveness, and general manufacturing high quality. Advanced cutting innovations play a crucial function in simplifying operations and enhancing the manufacture process. One of one of the most popular innovations in this area is the implementation of laser reducing systems. Laser cutting offers unmatched accuracy, allowing for complex styles and complex shapes to be cut with marginal material wastage. Furthermore, plasma cutting innovation has additionally revolutionized steel manufacture by making it possible for swift and specific puncturing electrically conductive materials. This approach is especially reliable for cutting thick steel plates with speed and precision. Water jet cutting is another innovative innovation that utilizes a high-pressure stream of water to puncture numerous types of products, including steel, with remarkable accuracy. By including these advanced cutting modern technologies right into steel fabrication processes, suppliers can dramatically raise efficiency, minimize manufacturing times, and inevitably boost the top quality of their products.
Automated Welding Solutions
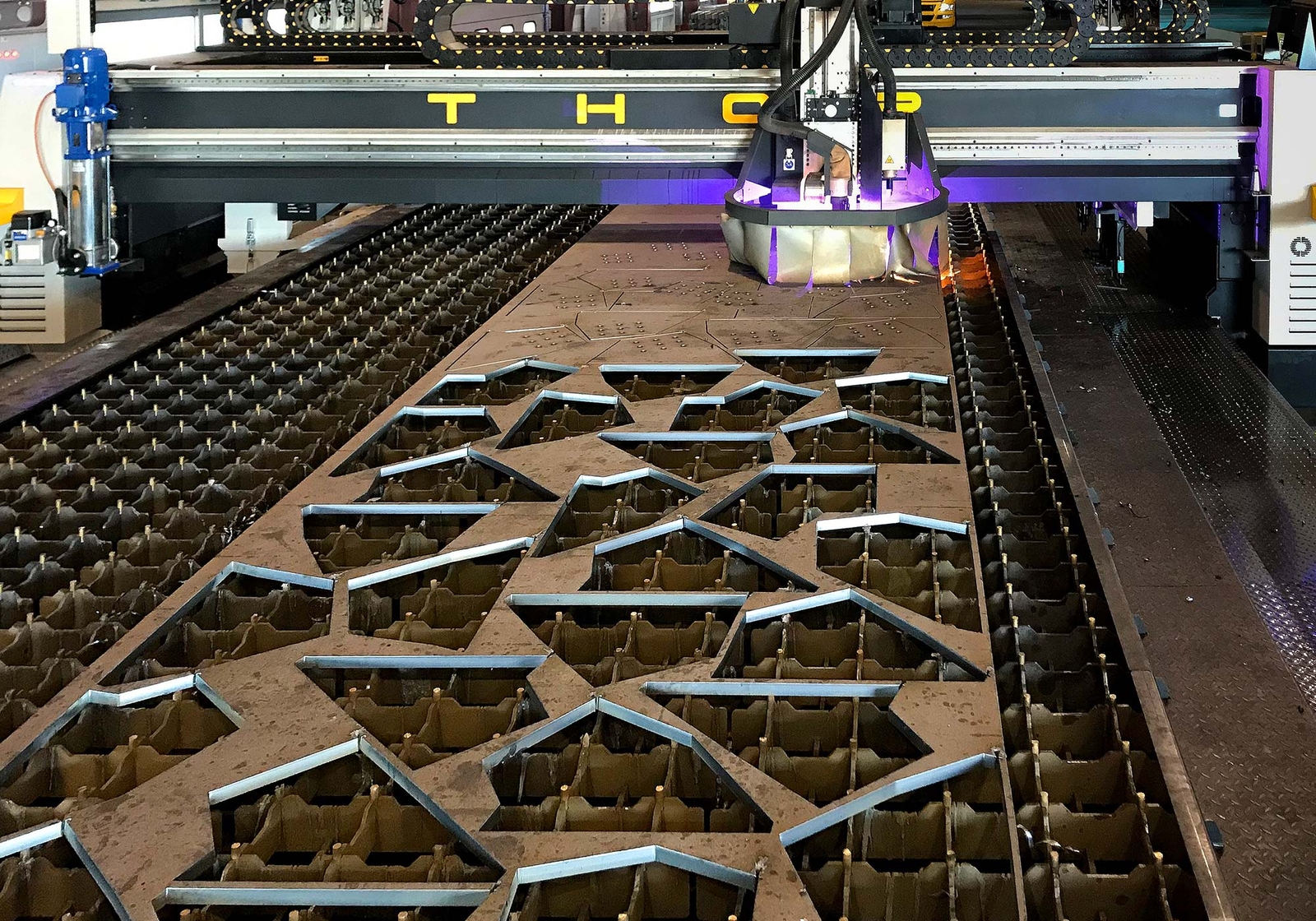
Among the essential advantages of automated welding systems is their capacity to maintain a high degree of precision throughout the welding process. The accuracy offered by these systems makes sure that welds are uniform and fulfill the needed requirements, resulting in more powerful and more reliable steel structures. In addition, automated welding systems reduce the risk of human error, causing fewer issues and remodel.
Furthermore, these systems can take care of complex welding jobs easily, including welding in tight rooms or on bent surfaces. This convenience makes automated welding systems ideal for a variety of steel fabrication applications, from large industrial projects to intricate custom-made layouts. In general, the execution of automated welding systems in steel fabrication procedures substantially boosts performance, quality, and general project outcomes.
Supply Management Solutions
Enhancing functional performance and simplifying procedures, efficient stock administration options play a crucial function in maximizing steel construction procedures. By applying robust inventory monitoring systems, steel manufacture business can make sure that the ideal materials are readily available when required, decreasing interruptions and delays in production timetables. Utilizing innovative software application remedies permits real-time monitoring of stock degrees, making it possible for accurate projecting of product requirements and stopping stockouts or overstock circumstances.
In addition, inventory management options assist in minimizing carrying expenses connected with excess supply and improve money circulation by lining up inventory degrees with real need. By classifying materials based upon use frequency and criticality, fabricators can prioritize purchase and storage room appropriation, even more improving functional effectiveness. Furthermore, executing barcode or RFID modern technology facilitates precise stock monitoring and streamlines the surveillance of material activities within the center.
Continual Process Improvement
To build on the gains made through reliable supply administration options, the emphasis now changes towards driving continuous procedure enhancement within steel fabrication procedures. Continuous procedure enhancement is an organized method targeted at boosting efficiency, lowering waste, and boosting general quality throughout the manufacture procedure. By executing a culture of continuous renovation, steel construction firms can recognize traffic jams, streamline operations, and maximize sources to make best use of site web efficiency.
One trick aspect of continual process improvement in steel fabrication is the normal evaluation and evaluation of manufacturing procedures. This includes gathering responses from employees, checking crucial efficiency indicators, and determining locations for enhancement. By leveraging data-driven understandings, firms can make enlightened choices to drive significant adjustments that favorably impact procedures.
Additionally, adopting lean manufacturing concepts can significantly add to process renovation in steel construction. steel fabrication melbourne. Methods such as value stream mapping, five organization, and Kaizen events can help eliminate non-value-added tasks, standardize procedures, and cultivate a society of technology and constant learning within the organization
Final Thought
To conclude, enhancing steel construction procedures for maximum efficiency needs mindful preparation, utilizing sophisticated cutting modern technologies, applying automated welding systems, managing stock successfully, and continuously enhancing processes. By incorporating these methods, suppliers can improve efficiency, minimize prices, and boost overall performance in the steel fabrication market.
With efficient format preparation, firms can eliminate bottlenecks, reduce production downtime, and enhance the total functional performance of the steel fabrication procedure. steel fabrication melbourne.
Using sophisticated modern technologies in steel manufacture procedures boosts accuracy, effectiveness, and general production high quality. By integrating these advanced cutting technologies right into steel manufacture procedures, makers can substantially boost effectiveness, decrease production times, and ultimately boost the top Discover More Here quality of their items.
In general, the implementation of automated welding systems in steel manufacture procedures substantially enhances efficiency, top quality, and total job outcomes.
One trick facet of constant process renovation in steel construction is the regular testimonial and analysis of production procedures. (steel fixing)
Report this page